Designing a one-part fully compliant eyeglasses frame for FDM 3D printing
Daan van Meurs
Access to eyeglasses in the global south has been identified as an urgent need. 3D printing is a cheap and an alternative for local manufacturing. However, a design tailored for 3D printing is needed; this is where the making comes in.
Access to eyeglasses in the global south is problematic and has been identified as an urgent need. Currently, in the developed world, a monopoly (Essilor Luxottica) dominates the frames industry. Using 3D printing, low price local manufacturing is possible without the need for complex production facilities or a highly educated workforce. A 3D Printer can print eyeglass frames in the global south for a fraction of the cost of those sold in the west.
We designed a one-part eyeglasses frame for 3D printing using a simple FDM 3D Printer. No assembly is required anywhere in the production process. To achieve this, we developed a compliant hinge design. The hinge is bi-stable (can open and close) and uses a flexible bending mechanism in combination with two stiff beams. When the hinge is pushed, the flexible mechanism bends and the beams slide over each other, resulting in resistance against the pushing. After pushing it beyond a certain point, the resistance is overcome and the hinge snaps into place. The difference in angles between the two stable states is exactly 90 degrees; this rotation was chosen as it is convenient for designing eyeglasses.
With a unique hinge design forming part of the eyeglasses frame, the whole frame can be printed as one part. This allows the temples of the glasses to be folded in and out, making the design as practical as existing eyeglasses design.
A one-part eyeglasses design that can be manufactured anywhere with a 3D Printer enables local manufacturing on any scale for a fraction of the price of conventional eyeglass frames. The lack of assembly means that almost no labour is needed.
Future directions: 3D scanning can be used to measure people’s head and face dimensions to generate a personalized frame for a perfect printer-made fit, with no need to visit a specialist to modify the frame.
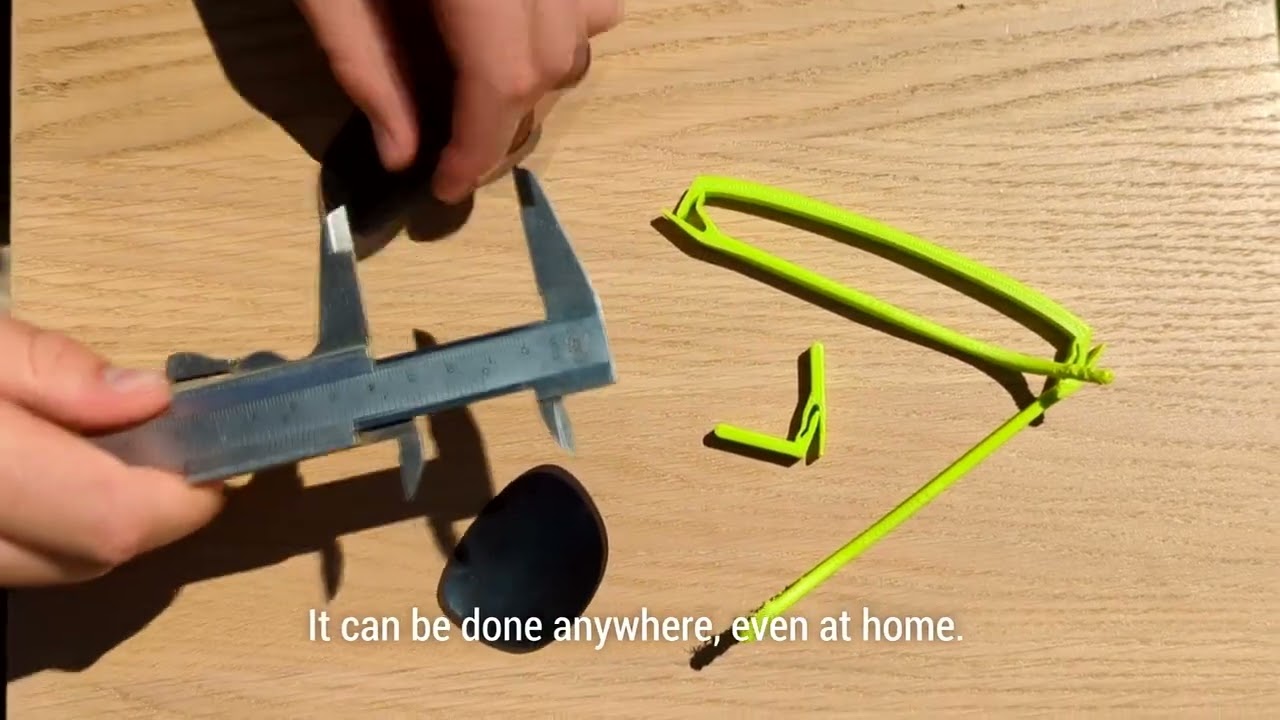